Abstract
Global gas process systems specialist Oxair has supported hundreds of medical facilities across the world by installing Oxygen Pressure Swing Adsorption (PSA) technology as a highly effective alternative to supplies of oxygen in cylinders. Be it United Kingdom’s National Health Service (NHS) or India’s Government and Private Hospitals, Oxair has come to the rescue of the medical fraternity with its supply of standard medical oxygen, vital for patients with respiratory conditions, who were under severe pressure due to the ‘twindemic’ of rising flu and COVID hospitalisations.
Oxair’s system delivers constant oxygen of 94-95 percent purity through PSA filtration, a unique process that separates oxygen from compressed air. The gas is then conditioned and filtered before being stored in a buffer tank to be used directly by the end user on demand. This case study explores in detail Australian company Oxair’s growth story and the strategic establishment of its global manufacturing facilities in India.
Introduction
The COVID-19 pandemic revealed a harsh reality: the desperate shortage of oxygen supply. As hospitals strained to meet the overwhelming demand, the life-sustaining gas became a symbol of the crisis. Families anxiously searched for oxygen cylinders, while healthcare workers battled to provide care with dwindling resources. Companies like Oxair became life saviours. During a worldwide shortage of medical oxygen supplies, Oxair’s Pressure Swing Adsorption (PSA) systems were installed in healthcare facilities ensuring a reliable supply of oxygen.
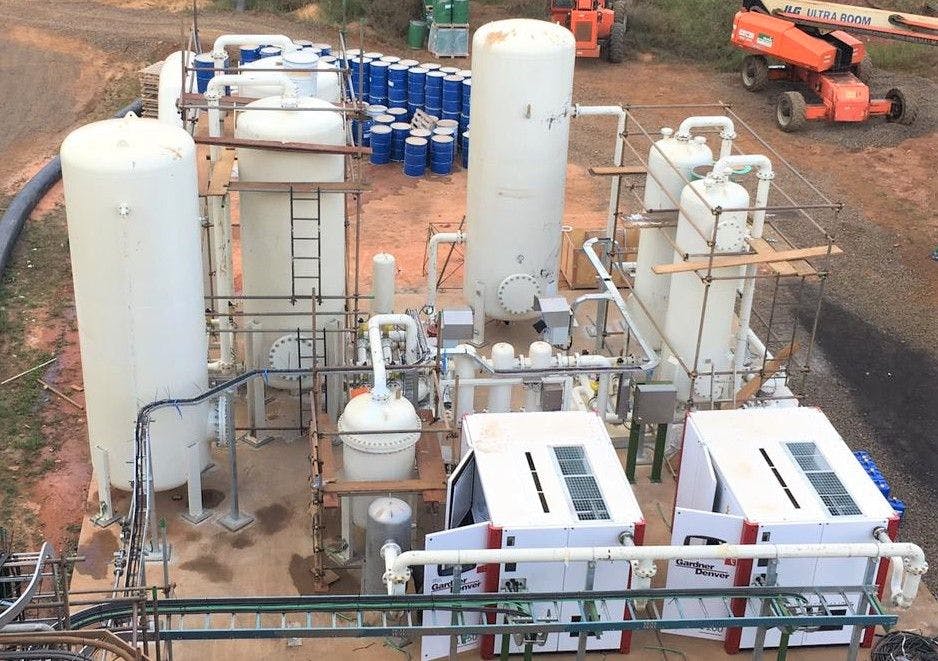
Oxair is a world-leading manufacturer of gas process systems for shipboard and land-based use. The company’s diverse product portfolio includes oxygen generator using unique PSA process, nitrogen generators, pressure vessels, nitrogen membrane systems, desiccant air dryers, mist eliminators, water separators, carbon adsorption with its core focus on safety, ease of maintenance, and offering cost-effective solutions into every international market.
Oxair’s gas process systems are used in a variety of industrial sectors including medical, gold mining, water treatment, oil and gas, food, chemical, biotech farming and aquaculture. Their Medical Oxygen PSA automated systems offer safety benefits by eliminating the logistical complexities and expenses associated with gas bottle shipments.
In gold mining, Oxair's systems deliver cost-cutting advantages by introducing oxygen into the gold leaching process, reducing cyanide consumption, or obviating the need for costly hydrogen peroxide. For the oil and gas sector, Oxair provides nitrogen generation systems that offer a cost-effective, continuous source of nitrogen for purposes like flare control, compressor operation, black start processes, and pipeline purging on gas plants.
In the food industry, Oxair offers nitrogen generators that play a pivotal role in preserving packaged foods such as fruits and vegetables, and in the gas flushing of meats to maintain their colour. This technique, known as MAP (Modified Atmosphere Packaging), hinges on Oxair's Proprietary Nitrogen Membrane Generators and Nitrogen Pressure Swing Adsorption Generator Systems, which can yield substantial savings of up to 50 percent over traditional supply methods.
Oxair's oxygen generators for water treatment deliver efficient performance in wastewater applications. By infusing oxygen into water treatment plants, these systems enhance sludge settling, reduce sludge loads, control odours, and enhance treatment capacity. They effectively eliminate complex organic molecules, cyanides, and phenols from chemical waste. It is also a leading manufacturer of pressure vessel filters and water separators for moisture and oil carry over in compressed air steam which, if ignored, can cause irreparable damage to plant and equipment.
Oxair Gas Systems is also urging the Australian mining industry to adopt the latest on-site gas generating technology to ensure a constant flow of nitrogen to keep truck tyres rolling, improve safety and reduce carbon footprint. Nitrogen’s composition makes it leak resistant. Nitrogen is also more resistant to heat build-up and reduces the risks from potential freezing at high altitudes, where tyres may be difficult to change or service due to the remoteness of the location or application.
India Strategy
In 2018, Oxair strategically selected Chennai, located in the State of Tamil Nadu, India, as the destination for its global expansion goals. The decision was supported by a combination of factors that underscored the region's suitability. Situated in proximity to a bustling port and a network of crucial suppliers, Chennai's significance as a logistics hub played a pivotal role. Also, the region's English-speaking workforce and a lower cost base contributed to the feasibility of Oxair’s venture. Moreover, Oxair's pre-existing decade-long partnership with an Indian company laid solid groundwork of familiarity and trust.
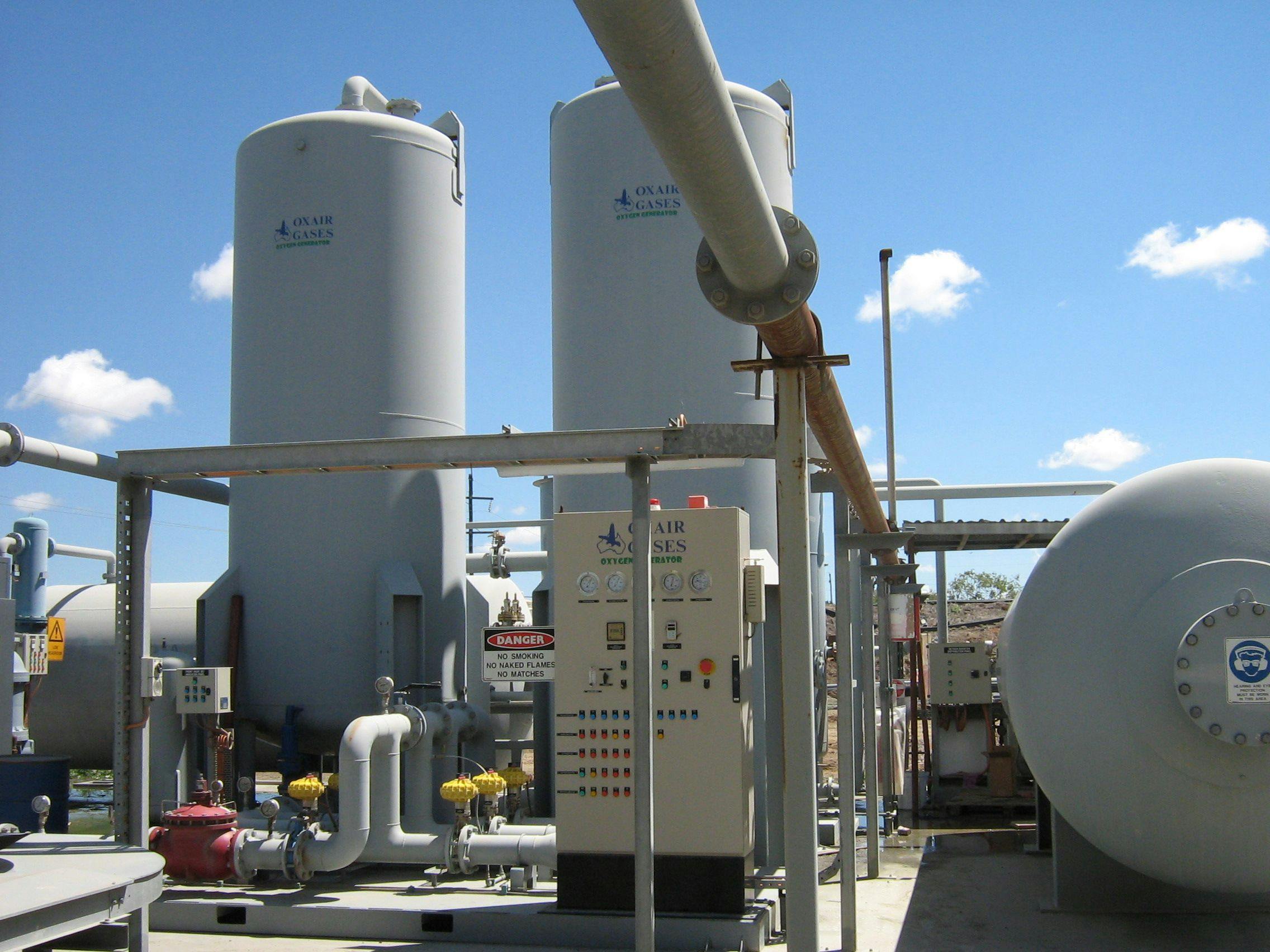
While Oxair's headquarters is in Perth, Western Australia, the company established two state-of-the-art manufacturing facilities in India. A significant portion of the engineering staff remains stationed in the Perth office, ensuring a seamless coordination between headquarters and manufacturing hubs. The financial operations, including accounting, remain centralised in Perth. An impactful strategic move was the relocation of the drafting office to India, further optimising the manufacturing process.
The rationale behind these developments was twofold. Primarily, Oxair sought to penetrate the Indian market while leveraging the manufacturing facilities to cater to international markets. To this end, the company structured two distinct entities in India.
The first, co-owned with a 30 percent local director and 70 percent Australian ownership, focused on manufacturing Medical Oxygen Systems for both domestic and international deployment. The second entity stands as a wholly Australian-owned enterprise, exclusively geared towards export operations. As of today, Oxair's workforce in India comprises of approximately 50 individuals, making a substantial contribution to local employment and the broader economy. In essence, Oxair's inspired expansion not only marked its presence in India but also underscored its commitment to bolstering local industry and global healthcare standards.
Their initial strategy yielded fair results, although necessitating a few adjustments along the way. Negotiating India's intricate tax and banking systems posed occasional challenges. Especially, establishing robust supply chains presented a formidable hurdle, as the prevailing business landscape in India rarely adheres to credit systems, demanding a higher operational cash flow. Adapting local manufacturers to Oxair's elevated quality standards emerged as a significant obstacle, compounded by the perpetual challenge of determining superior quality. These challenges, by no means swiftly resolved, demanded years of dedicated effort to elevate the local workforce to the desired proficiency levels.
Moreover, interfacing with suppliers further enhanced the complexity. Oxair discovered that it was imperative to instil quality consciousness in these partners, educating them on the nuances of quality control. The disparities are particularly pronounced in critical areas such as electrical wiring standards, welding practices, and pressure vessel construction.
“Getting them to adjust to quality standards is a major hurdle. These are not overnight fixes and takes years to get your own people to the level you want them to be at.” – James Newell, Managing Director, Oxair Gas Systems Pty Ltd
Oxair has embarked on an ongoing journey of training its workforce on multifaceted issues. Their comprehensive process involves educating not just their own personnel, but also extending that knowledge and transferring it to their suppliers. The journey is one of persistence, refining the operational landscape with commitment to quality and excellence.
“I think we have installed something like 200 systems. Two years ago, I signed a 15-year contract with two of the world’s, largest Gas companies operating in India to supply and maintain medical oxygen systems for their customers.”
During COVID, Oxair’s manufacturing factory in Chennai ensured oxygen plant supplies to the Indian government’s public and private hospitals, charities, and corporates including Tata Group, Aster Group of Hospitals, Hiranandani Hospital, Agrasen Hospitals, Vijaya Hospitals, Indian Navy, District hospitals in Telangana and Andhra Pradesh, Govt. of Maharashtra and Rotary Group to name a few.
“Setting up supply chains is a major hurdle as most companies in India do not work on a credit system, so you need more cash to operate a business there.”
Seeing The Future
As the sole director and stakeholder of the company, James Newell's decisions were free from internal barriers. He emphasises the importance of thorough preliminary research: finding a reliable partner and selecting an optimal location hinging on market expectations, whether for local consumption or global export, each presenting its distinct set of challenges.
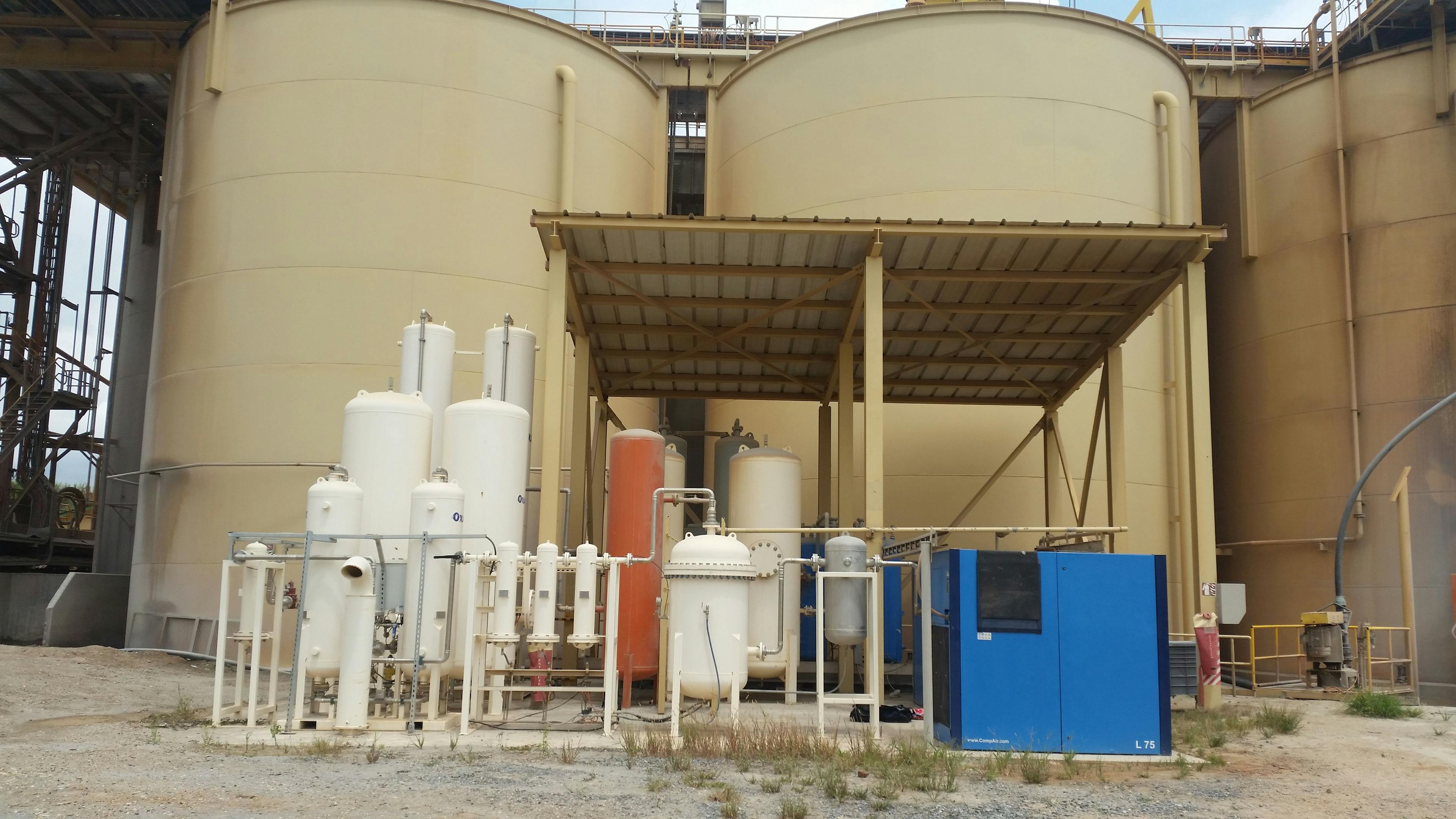
“Covid allowed us to grow the business exponentially, however Covid also stopped us growing and finalising our business model internally.”
Oxair is a perfect example of India’s ‘Make in India’ potential, and how Australia’s technologically advanced manufacturing expertise could be entwined with Indian skills to maximise on scale and existing opportunities. The Indian government’s ‘Make in India’ initiative was launched globally in September 2014 as a part of India’s renewed focus on Advanced Manufacturing. The objective of the Initiative is to promote India as the most preferred global manufacturing destination, with an aim to make India an integral part of the global supply chain. It is designed to facilitate investment, foster innovation, enhance skill development, protect intellectual property and build best in class manufacturing infrastructure in the country. The primary objective of this initiative is to attract investments from across the globe and strengthen India’s manufacturing sector.
The program also aims at improving India’s rank on the Ease of Doing Business index by eliminating the unnecessary laws and regulations, making bureaucratic processes easier, making the government more transparent, responsive and accountable. The Make in India program focuses on 25 strategic sectors. These include automobiles, automobile components, aviation, biotechnology, chemicals, construction, defence manufacturing electrical machinery, electronic systems, food processing, IT & BPM, leather, media and entertainment, mining, oil and gas, pharmaceuticals, ports and shipping, railways, renewable energy, roads and highways, space, textile and garments, thermal power, tourism and hospitality and wellness.
Australia’s advanced manufacturing accounts for around half of Australia’s A$100 billion plus annual manufacturing output and is one of the fastest growing export sectors. Part of this success is due to cross-fertilisation between R&D institutions and the manufacturing sector. India can explore synergies with Australia in advanced manufacturing as part of ‘Make in India 2.0’ (which includes segments such as robotics, genomics, chemical feedstock and electrical storage). Advanced manufacturing technologies today are vital to gain global competitiveness in cost, speed, innovation and quality.
Australia’s strength lies in high-value, low-volume manufacturing with emphasis on design, research and development, and innovation in the production process. These sectors offer considerable opportunities to Australian companies to consider establishing manufacturing operations in India. With a large consumer market, skilled workforce, cost-effective labour, available incentives and subsidies and opportunities for global supply chain integration – India’s manufacturing potential could be used for scaling exports to international markets as well as capitalising on the domestic market gains.
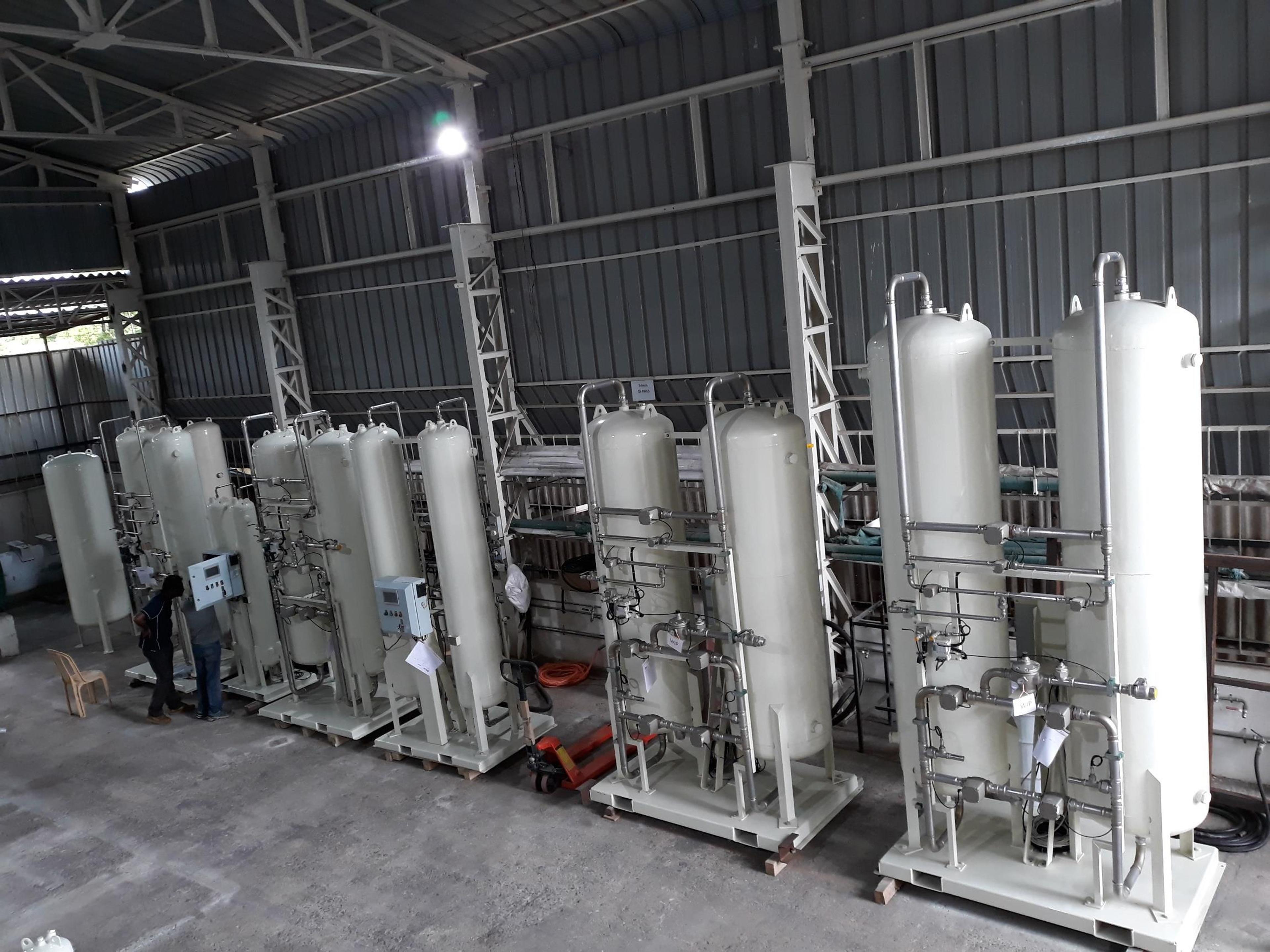
Planning Ahead
The journey of Oxair's India expansion offers valuable insights into complexities and opportunities of entering a new market, and key learnings for companies keen to set up manufacturing operations in India. These include —
- Focus on meticulous research and planning. Choosing the right partner and location aligned with the desired outcomes (local market or export) is crucial and has a significant impact on the business's trajectory
- Understanding and navigating the intricacies of India's tax, banking, and regulatory systems is paramount. These areas demand adaptability and the ability to overcome hurdles to establish a seamless operation
- Establishing robust supply chains is pivotal for business sustainability. The absence of credit systems in scenarios, underscores the importance of adequate working capital to support operations effectively
- Raising local partners to global quality standards requires consistent effort. Ensuring transparent communication about changes and consequences is vital to avoiding disruptions caused by uncommunicated decisions
- India's workforce is characterised by strong work ethics and loyalty. The stability of the workforce can be an advantage compared to transient labour markets in other regions
- Incorporating safety practices into the workplace is essential due to existing gaps in safety protocols. Ensuring high-quality standards and safety education improves overall operations and contributes to employee well-being
- Communication can still pose a challenge, even when a shared language like English is used. Acknowledging and understanding cultural nuances can enhance effective communication and collaboration
- Managing expectations of urgency in various aspects of operations is important. Recognising that decision-making and response times might differ, from what is typical in other markets, is crucial for effective management.
Overall, Oxair's India story underscores the significance of strategic planning, adaptability, and a commitment to maintaining high standards while navigating the intricacies of a new market.
The global manufacturing industry is at the cusp of major technological transformation, and Australia and India can be dependable partners in this journey. India’s need for global competitiveness in the manufacturing sector can be matched with Australia’s innovation and capabilities in advanced manufacturing. India could equally supplement Australia’s need for cheaper production costs and high-volume needs. Australia can expand at two levels. First, manufacturing in India, in a cost-competitive environment due to the ample availability of raw materials, cheaper production cost and labour, could be the key for Australian companies to expand their footprint to other parts of the world. ‘Designed in Australia – Made in India’ can be the new focus area for this partnership. Second, Australia’s advanced manufacturing offers great opportunities to Indian manufacturers to access new technologies. The changing operational dynamics in the COVID-19 scenario have pressured businesses to de-risk all segments of operations, hence the transition to industry 4.0 and automation has also become important.
The future of manufacturing depends on operating seamlessly across all channels, including manufacturing, inventory, supply chain, marketing, sales and distribution. Core to changes will be a symbiosis between traditional and advanced manufacturing. Co-create, co-innovate and co-produce should be the way forward for the Australia-India relationship in manufacturing.